I'm very pleased to have the one and only Andrew Scheps on my latest Inner Circle podcast. Andrew has a long list of great mixing credits, from the Red Hot Chili Peppers to Adele to Metallica to Justin Timberlake and many more, and is one of uber-producer Rick Rubin's go-to mixers.
You can hear us talk about everything from mixing in the box, to parallel compression, to his approach to recording, to Andrew's very cool presentation on hi-res audio.
On the show intro, I'll talk about the study to find out who is actually buying all the vinyl that's being sold, and the super quick way to a onstage monitor mix or studio cue mix.
Remember that you can find the podcast either on iTunes or at BobbyOInnerCircle.com, and now also on Stitcher.
Help Support This Blog
Friday, January 9, 2015
Thursday, January 8, 2015
Fleetwood Mac "Go Your Own Way" Isolated Vocals
It's Friday again and that means it's time for another isolated track. Today we'll listen to the isolated vocals from Fleetwood Mac's big hit "You Can Go Your Own Way, (this is a Spotify link)" the first single from the band's huge 1977 Rumours album. Here are some things to listen for (the track starts at 0:07).
1. Check out all the the breaths on the track. You can hear lead singer Lindsey Buckingham take a big breath of air before most vocal phrases, and the whole band before each harmony chorus. We'd probably delete these today in our DAW world.
2. There's a nice medium length delayed reverb on the vocals. There's more there than what you think is there when you listen with the instrumental track.
3. The lead vocal is at the top of the harmony stack, which is somewhat unusual.
4. The harmonies begin to get sloppy with the releases towards the end of the song at 3:30. You can hear all vocalists ending the phrases at different times, which doesn't happen earlier on.
1. Check out all the the breaths on the track. You can hear lead singer Lindsey Buckingham take a big breath of air before most vocal phrases, and the whole band before each harmony chorus. We'd probably delete these today in our DAW world.
2. There's a nice medium length delayed reverb on the vocals. There's more there than what you think is there when you listen with the instrumental track.
3. The lead vocal is at the top of the harmony stack, which is somewhat unusual.
4. The harmonies begin to get sloppy with the releases towards the end of the song at 3:30. You can hear all vocalists ending the phrases at different times, which doesn't happen earlier on.
Wednesday, January 7, 2015
The Speaker That's So Loud It Can Kill You
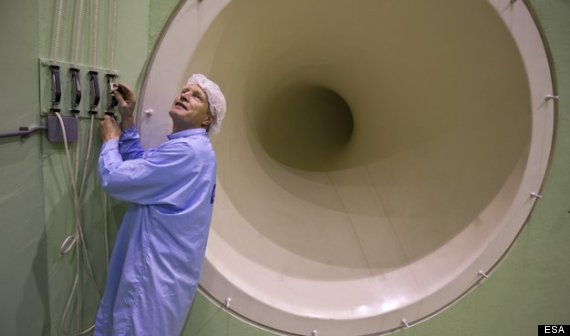
It's actually a test chamber called the Large European Acoustic Facility (LEAF) and was built by the European Space Agency for a single purpose - to make sure that satellites can withstand the effects of the massive noise made by a rocket during liftoff.
The chamber is 54 feet high, 36 feet long and 30 feet deep (you only see part of one horn on the left, but you can see most of it on image on the right), and consists of 4 different horns with cutoff frequencies of 25Hz, 35Hz, 80Hz and 160Hz. The frequency response extends out to 10kHz.
The system uses 100% nitrogen gas to activate it so that micro-climates aren't created and cause rain to form inside the chamber. As a safety precaution, it can only be activated once all the doors are closed, and both doors and walls are steel-reinforced.
The overall SPL can reach 155dB, which would instantly perforate your eardrums, then cause your lungs to vibrate so violently that they'd rupture, and you'd probably have a heart attack as well, so don't try this at home!
Tuesday, January 6, 2015
The Ins And Outs Of Road Cases
I recently received a few questions about road cases so I thought this is a good time to bring back something that I posted about few years ago. It's an excerpt from The Touring Musician's Handbook that provides a good look at the differences between popular road cases.
"For many musicians, buying road cases for their gear is sort of a right of passage. As soon as you stencil your name on the cases, it suddenly means that your stock as a musician has risen and you’ve made the jump to becoming your own brand.
While some players choose not to case up their gear in order to save money in the beginning of their touring career, they soon see the shortsightedness the first time a favorite instrument is damaged from a fall off of a ramp or loading dock. Road cases are not only worth it, but almost mandatory in that your gear always has to work, and the only way to assure that happens is to keep it protected from the frequent and many knocks of the road.
The ATA Standard
Although many cases may look similar, the sturdiest (and consequently most expensive) ones are what’s known as ATA cases. This is a design based on an airplane parts packaging specification (known as ATA 300 Category 1), developed by airline packaging engineers and certified by the Airline Transport Association. ATA 300 compliant cases are designed to withstand the rigors of being shipped a minimum of 100 times, and specifies that the case will have recessed handles that will not break during transit. The standard also details the level of quality of every piece of construction material that goes into the case, including locks, hinges, and fastening systems, and also states that all rivets and screws must be non-corrosive and all edges must be rounded and have certain level of construction quality. Because of this ATA standard, the typical road case has also come to be known by the name “flight case,” since it’s made principally to survive multiple flights.
Tip: If the road case is too heavy for a single person to carry it, it needs casters.
Types Of Road Cases
Road cases come in a lot of different styles and a lot of different materials. As a result, all road cases are not created equal. Some are great for keeping the weather off your gear, while others are built to withstand the constant battle of the road. Let’s take a look at the different types.
Fiber Cases - Fiber cases are the typical drum cases that most drummers have used some time during their life (see Figure 7.2). They’re made out of fiberglass reinforced polyester and are very strong and rugged. While they work great for the club musician or weekend warrior because they keep the scuffs and incidental scratches off of the instrument, they’re deficient for road work in several ways; there’s little or no shock mounting for the instrument, the case is closed with a nylon strap that can be cut or lost, and their irregular shape make them difficult to pack efficiently. This means they usually get tossed on the top of the evenly packed square cases in the truck where they bounce around a lot as a result. Guess what that does for the instrument? They’re also prone to caving should something very heavy be placed upon them.
Aluminum - Aluminum cases have a major advantage in being extremely light weight, and usually have a fair amount of shock absorption (see Figure 7.3) inside. That being said, they’re very easy to pierce, and should generally not be used for shipping purposes as a result. It’s possible to have an ATA standard aluminum case, but you have to use so much aluminum that you lose the weight advantage that aluminum has over other types of cases.
Carpet Cases - These are simple plywood cases with an outer fuzzy carpet material (see Figure 7.4). This type of construction once again offers little in the way of impact relief and protection. They’re heavy because the internal frame may be constructed of steel, and even though the carpet finish makes them very tough, there’s not much in the way of shock mounting. Carpet cases are great for things like cables and mic stands, but not for anything expensive that must be protected.
Molded Plastic - Some cases are made out of molded plastic (see Figure 7.5) which might be good for keeping the rain off an instrument but not much help under the repeated impacts of being loaded onto a truck. Their weakness frequently is in the latches, which can break or come loose over time, and you don’t see plastic cases in very large sizes. Once again, molded plastic cases may come in an odd enough shape that it won’t easily pack in the truck. There are ATA molded cases made, which are also mil spec for military electronic gear, but they’re really expensive and generally custom made.
Sandwiched Material - The strongest and most common road cases are the ones with sandwiched material and reinforced edges and corners (see Figure 7.6), and these can be made of different materials for different types of transit. Most sandwich-type road cases are constructed in three main layers:
- an outer layer of a plastic-based laminate called ABS
- a middle layer of 3/16 to ½ inch cabinet-grade plywood such as birch, poplar or maple
- an internal shock-absorbing foam layer that corresponds to the exact shape of the instrument or piece of gear.
- The edges of the case are reinforced with aluminum extrusion, and have steel or zinc corner pieces and recessed handles and fasteners.
Protective Foam
There are generally two types of protective foam used in road cases. Polyurethane foam is very soft and provides a gentle cushion for any delicate item. It’s usually available in ½ inch to 10 inch thickness in ½ inch increments. The problem is that it’s so soft that it can be crushed by a heavy item, in which case a polyethylene foam is used instead. Polyethylene foam is very dense and not very flexible, and the texture is almost like plastic. Frequently it’s used under a heavy item where polyurethane would simply not last due to the constant compression. Usually you want at least a half-inch of foam between your instrument and the outer layer of the case, although most people prefer one inch for added protection.
One thing that’s mostly overlooked with road cases is that the internal foam layer can have some negative chemical interactions with the finish of your instrument that can cause it to become dull and discolored over time. Nitrocellulose lacquer (like those used on vintage guitars), varnish and shellac are much more susceptible to this than the modern polyurethane and polyester type finishes. The way to prevent any interaction from occurring is to make sure that your road cases have a cloth lining over the foam (see Figure 7.7). Some companies use a velvet-like material layer mostly for cosmetics, but it will also protect your instrument from any finish damage from the foam. If buying a custom case, a cloth covering only adds a small amount to the overall cost of the case.
Remember, if you buy good quality cases, they can last for your entire career on the road, so go for the best and don’t cheap out.
Tip: When buying road cases, try to buy either cases already in stock at your local music store or pro audio dealer, or have them made locally. The cost of shipping them can sometimes be almost as much as the case itself. Almost every city now has a company that makes road cases, so finding one that’s local should be easy.The good thing about ATA type road cases is that they can be repaired. Just about anything can be replaced and the case will come back as good as new. In fact, there are companies that specialize in repairing road cases like Mobil Flight Case Repair, although just about any road case manufacturer can do it."
To read additional excerpts from The Touring Musician's Handbook and my other books, go to the excerpts section of bobbyowsinski.com.
Monday, January 5, 2015
Yogi Horton's Funk Drumming And History Lesson
This is one of the best instructional videos I've ever seen. Not only is it a lesson in funk drumming, it's a history lesson as well. It features the late great funk drummer Yogi Horton, who played on more than 100 albums for artists like Luther Vandross, Ashford and Simpson, Dianna Ross, Aretha Franklin and many more. Even non-drummers will like it.
Labels:
funk drumming,
Luther Vandross,
video,
Yogi Horton
Sunday, January 4, 2015
New Music Gear Monday: Audio-Technica SonicPro In-ear Headphones
In-ear headphones have become more and more a part of our lives, from the everyday use with our phones to listening to a monitor mix on stage. While there are some pretty good models available, most owe their sound to precision materials and manufacturing rather than sonic innovation. The new Audio-Technica SonicPro series tries an old loudspeaker idea for the first time in an in-ear monitor, and that's why they're worth checking out.
The AT SonicPro series features 5 models that were built for a high-quality audio experience by employing a push-pull driver system to increase the detail in the mid and high frequencies. The two 13mm drivers face one another but are wired out of phase to lower the distortion and increase the output sensitivity. As an example of the extended frequency response, the most expensive of the models, the ATH-CKR10, has a frequency response that goes out to an impressive 40,000Hz.
The ATH-CKR10 has a US retail of $389.95 (click for better price), the CKR9 is $269.95, and the CKR7 is $134.95. Two lower priced models, the CKR5iS and the CKR3iS are meant for smartphone use and feature integrated volume control and microphone, and are designed to nestle in your ear without entering your ear canal. They're priced at $64.95 and $39.95. All SonicPro models come with 4 sizes of silicone eartips and a two foot cable. You can check them out on the Audio-Technica site.
The video below gives a look at how the push-pull drivers work.
The AT SonicPro series features 5 models that were built for a high-quality audio experience by employing a push-pull driver system to increase the detail in the mid and high frequencies. The two 13mm drivers face one another but are wired out of phase to lower the distortion and increase the output sensitivity. As an example of the extended frequency response, the most expensive of the models, the ATH-CKR10, has a frequency response that goes out to an impressive 40,000Hz.
The ATH-CKR10 has a US retail of $389.95 (click for better price), the CKR9 is $269.95, and the CKR7 is $134.95. Two lower priced models, the CKR5iS and the CKR3iS are meant for smartphone use and feature integrated volume control and microphone, and are designed to nestle in your ear without entering your ear canal. They're priced at $64.95 and $39.95. All SonicPro models come with 4 sizes of silicone eartips and a two foot cable. You can check them out on the Audio-Technica site.
The video below gives a look at how the push-pull drivers work.
Subscribe to:
Posts (Atom)